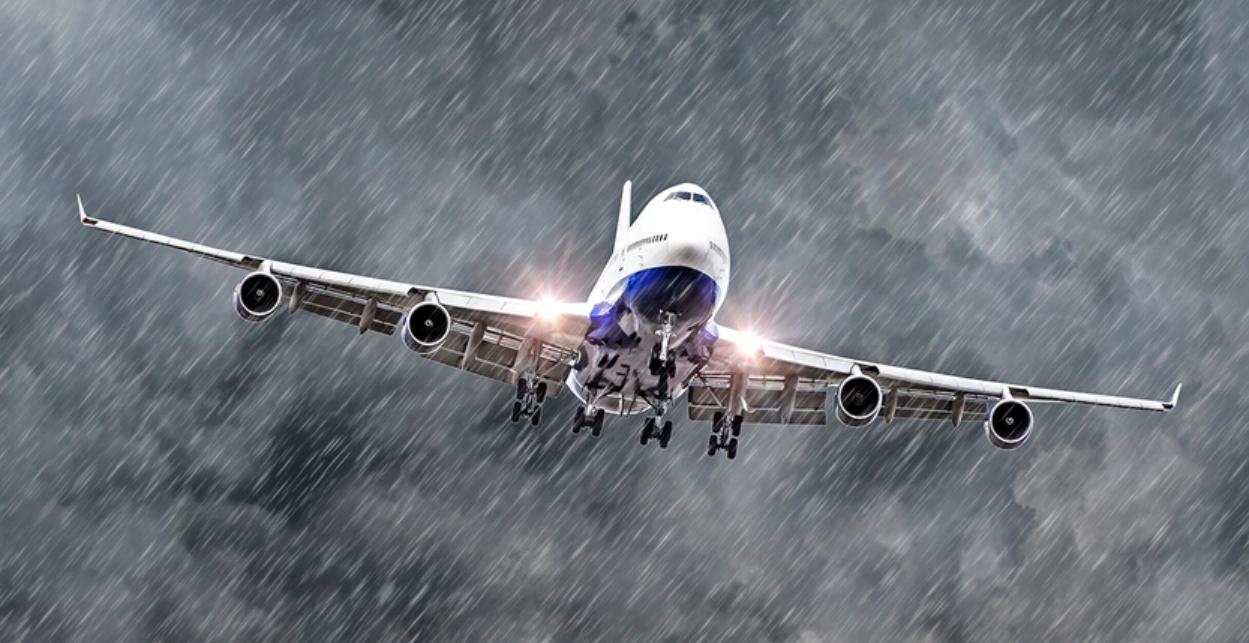
Water does not support combustion – this is a well-known fact. However, you will never see any sort of filter in front of aircraft engines to keep water from getting in, so why don’t they stall when it rains?
If the car engine is protected from rain water by a special design of the air intake, then it is not possible to install something similar in front of the aircraft engine. Moreover, even placing bird nets in front of the engines is impossible for some reason (see the link to the relevant material at the end of the article).
A typical jet engine passes up to 1,000 cubic meters of air through it every second. According to rough estimates, during a rain, 1 m³ of air contains on average a little less than 1 cm³ of water, which is not as much as it might seem to a person caught in a downpour. But this is due to the fact that water drops fall to the ground at a speed of 9 m / s, that is, during rain, every second, water contained in 9 m³ of air above it falls on a square meter of land.
It follows from the calculations above that ~ 1 liter of water enters the engine of an airliner caught in the rain every second. This volume is not capable of causing any harm, since during the mandatory tests of engines, their ability to “digest” up to 4.5 tons of water per minute, or 75 liters per second, is checked. During this test, the engine should not be damaged or stop working, but how is this possible?
First, not all of the air flow captured by the blades of a turbofan engine is sent to the combustion chambers. The typical bypass ratio in the case of passenger airliners is 10 to 1. This means that 10/11, or 91% of the air entering the engine is directed not to the combustion chambers, but to a through external circuit, which is used to increase the overall engine thrust.
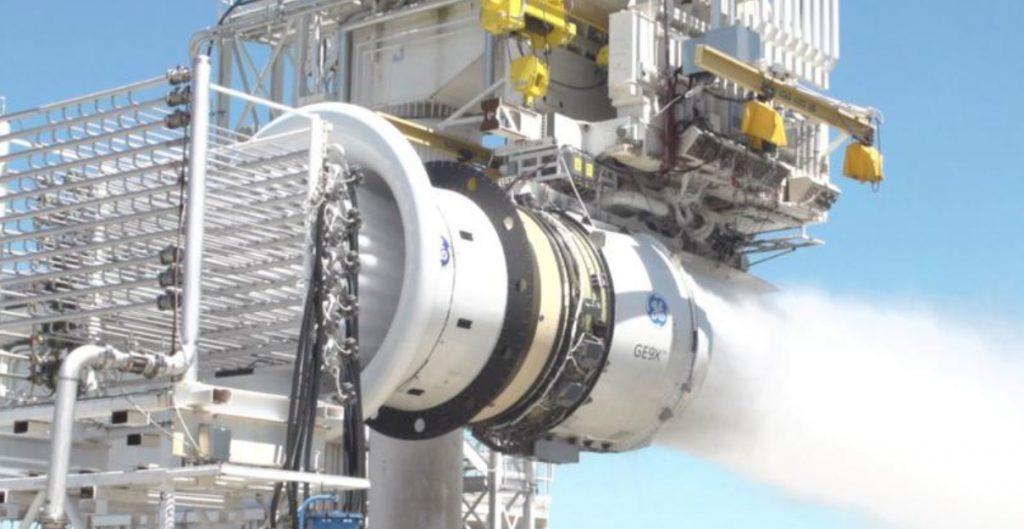
At the same time, during rain, the fan acts as a large centrifuge. And since water is heavier than air, under the action of centrifugal force it is directed mainly to the external circuit, where no combustion occurs.
Secondly, before entering the combustion chamber of an aircraft engine, the air (along with a small amount of remaining water) passes through the compressor. There, with increasing pressure, the air is heated to temperatures of around 260°C. The evaporation of water in this process is not capable of causing such a significant cooling that would prevent further operation of the engine.
In some cases, water cooling can even be useful, so it was also used in civil aviation. For example, early versions of the Boeing 707 and 747 were powered by Pratt & Whitney engines that used water injection. Additional cooling allowed the engines to develop more thrust, which was necessary during takeoff. Later, as the power of aircraft engines grew, water injection was abandoned as unnecessary.
If the water in the event of rain does not pose a threat to the aircraft, then the situation changes dramatically when the water freezes, turning into hail. It can not only damage the fuselage and glass in the cockpit, but also completely disable the engines. Fortunately, this phenomenon is quite rare, and pilots (almost always) successfully avoid it using weather radar data.